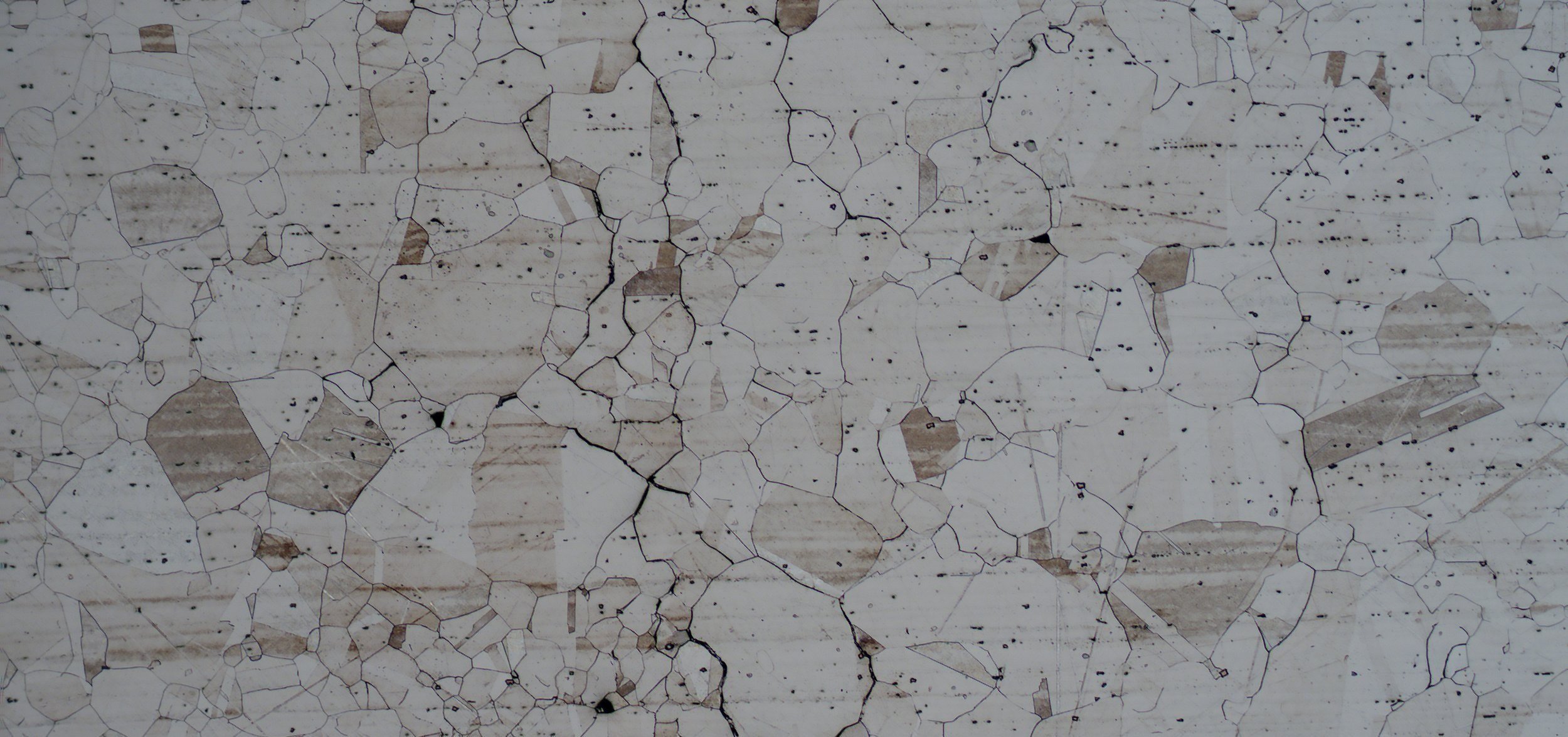
INSIDE INTELLIGENCE
TAILORED SOLUTIONS WITH PURPOSE
Empowering teams with tailored solutions that ensure safety and reliability through seamless communication.
At Met-Forensics, we understand that safety and reliability stem from delving beneath the surface. Our expertise lies in uncovering and addressing the hidden challenges within your process units. With decades of proven proficiency in mechanical integrity engineering, our team delivers cost-effective, customized solutions to enhance your plant's mechanical integrity—whether through proactive prevention or reactive resolution.
Met-Forensics Advantages
Resourcing
Our experienced engineers handle every aspect of your project
Customization
We tailor our approach to your assets, focusing on high-value areas that deliver the best return on investment.
Holistic
Our holistic approach ensures comprehensive mechanical integrity, boosting reliability, safety, and empowering teams to tackle critical challenges
Meet Met-Forensics
Cameron Curtis
With over 11 years of experience in corrosion and materials engineering, Cameron specializes in solving unique chemical and corrosion challenges, driving mechanical integrity and safety improvements for your site.
Clay Brittain, PE
Over 14 years of experience solving mechanical integrity challenges for upstream and downstream owner-operators.
Mark Hume
Over 10 years of experience as a manager, engineer, and software product owner.